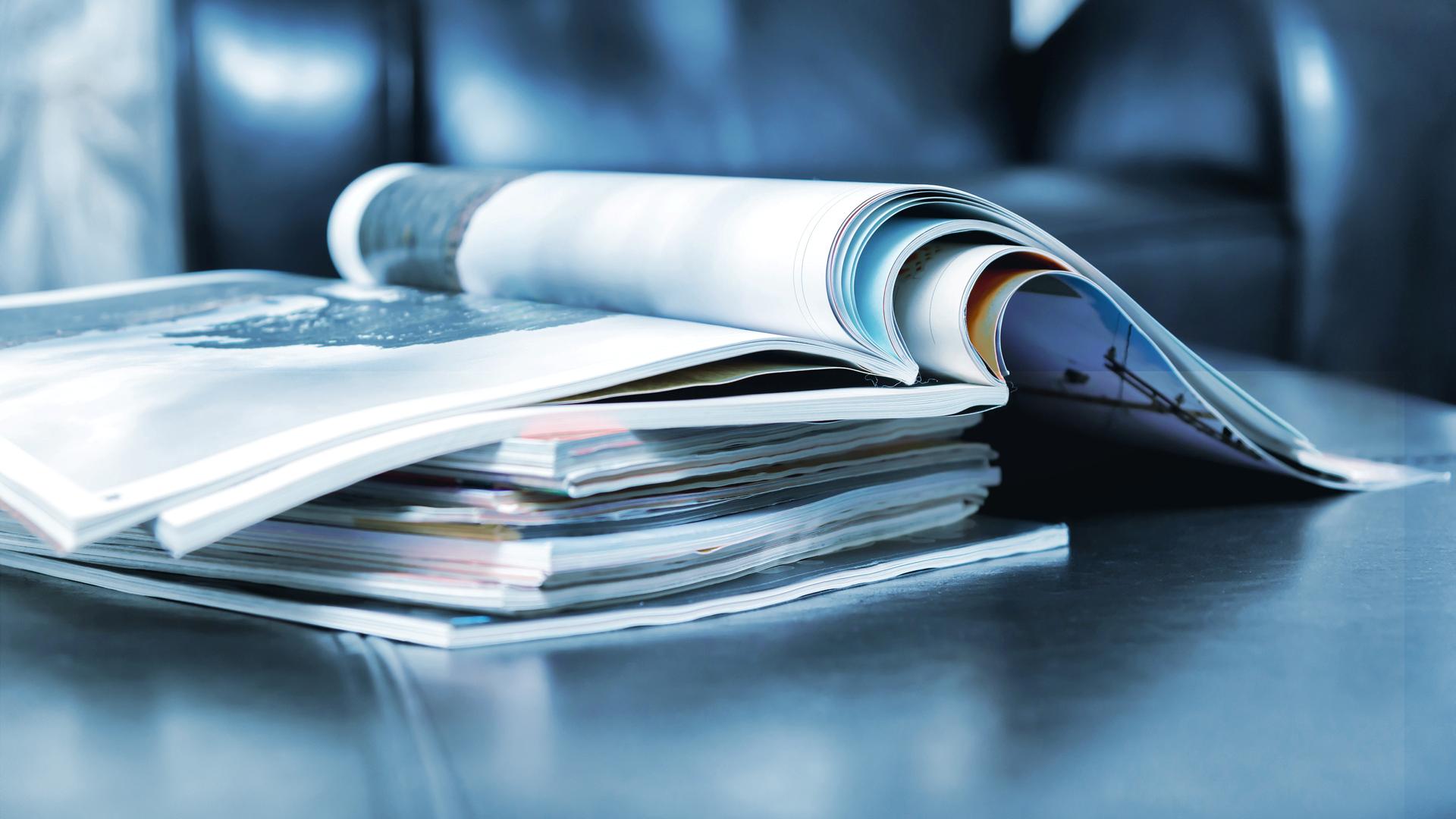
viastore automatise l'usine Electrolux au Brésil
Matériel et logiciel pour Curitiba
Dans le cadre de la restructuration de son usine de Curitiba, Paraná, au Brésil, le fabricant d'appareils électroménagers Electrolux est passé à un entrepôt entièrement automatisé. La verticalisation littérale des stocks a augmenté la productivité, réduit les coûts de 38% et standardisé les processus du groupe électrique.
Avec des marques comme Electrolux, AEG, Anova, Frigidaire, Westinghouse et Zanussi, le groupe Electrolux vend chaque année plus de 60 millions de produits pour les cuisines privées et professionnelles dans plus de 120 marchés. Le groupe emploie 52 000 personnes dans le monde entier. Au Brésil, Electrolux est présent dans environ 38 millions de foyers. En 2017, l'entreprise a continué à développer ses activités en Amérique du Sud grâce à l'acquisition de la marque Continental. Dans le cadre d'un processus global de reengineering visant à moderniser ses usines, l'acteur mondial a également réorganisé la logistique de stockage sur le site brésilien de Curitiba. La solution de manutention et de stockage entièrement automatisée a été réalisée par l'intégrateur de systèmes international viastore.
Trois options de restructuration étaient disponibles : Electrolux a d'abord envisagé d'augmenter la capacité de l'entrepôt existant et l'utilisation d'un entrepôt externe a également été discutée. "Cependant, du point de vue des coûts et des bénéfices ainsi que du point de vue technique, un nouvel entrepôt automatique était la meilleure solution", explique João Nilton Costa, Inbound Logistics Manager chez Electrolux.
Le choix s'est porté sur viastore parce que le spécialiste de l'intralogistique répondait le mieux aux exigences techniques : Le nouvel agencement combine un entrepôt automatique pour petites pièces (AKL) avec un entrepôt de palettes et utilise de manière idéale les 4000 mètres carrés de surface de stockage : D'une part, environ 6 720 palettes de marchandises de détail s'empilent sur une hauteur de 35 mètres : quatre transstockeurs, deux à simple profondeur et deux à double profondeur, se chargent de l'entrée et de la sortie dans l'entrepôt de palettes.
D'autre part, l'AKL de 14 mètres de haut a une capacité de 17 600 bacs et cartons. Pour la manutention, cinq autres transstockeurs à double profondeur sont utilisés. Leur dispositif de prise de charge "Multigripper" permet de charger et de décharger des porte-charges de différentes tailles et types de matériaux.
Parallèlement au système de stockage, viastore a installé à Curitiba la technique de convoyage appropriée : celle-ci ne transporte pas seulement des cartons ou des palettes dans et hors de l'entrepôt. Des systèmes de contrôle intégrés enregistrent également les dimensions et le poids des supports de charge transportés. Les données recueillies aident à déterminer l'emplacement de stockage idéal ou à stocker les palettes en fonction de leur catégorie de poids - jusqu'à 600 ou 1200 kilos.
"Nous avons pu réduire nos coûts logistiques de 38% en optimisant les itinéraires, en éliminant les inefficacités et en standardisant les processus", explique Costa. "De plus, l'automatisation permet la gestion visuelle des données, ce qui accélère considérablement la prise de décision".
Le stockage centralisé des matières premières a apporté des avantages décisifs à Electrolux. Grâce à une vue d'ensemble précise des stocks, l'approvisionnement des lignes de montage est garanti à tout moment. De plus, le haut degré de standardisation et de synchronisation réduit les distances de livraison nécessaires pour le stockage et le déstockage.
"Quand nous parlons d'efficacité, cela inclut la durabilité", souligne le responsable Inbound Logistics d'Electrolux. "Car si nous effectuons plus de tâches avec moins d'efforts et en moins de temps, nous économisons des ressources et sommes donc plus respectueux de l'environnement".
Pour gérer son entrepôt, Electrolux a recours à l'ensemble des fonctions du système de gestion d'entrepôt (WMS) viastore viadat : la solution logicielle fonctionne à la fois comme système de contrôle d'entrepôt (WCS) et comme système de flux de marchandises (MFS). D'une part, il gère l'ensemble de l'entrepôt et constitue le lien avec l'ERP existant, mais d'autre part, il régule également le flux de matériaux dans le processus d'entrepôt le long des convoyeurs. De plus, viadat gère le flux de matériel et communique avec l'API pour que les composants respectifs fonctionnent correctement. viadatVISION permet d'avoir une vue d'ensemble de tout l'entrepôt. Le logiciel surveille et visualise l'installation, gère les dispositifs de sécurité, localise les erreurs et aide à les résoudre.
"Notre objectif est de regrouper tous les processus de l'intralogistique dans un élément de contrôle central grâce à un système de gestion numérique", conclut Costa. "Les informations générées par l'entrepôt n'aident donc pas seulement à surveiller et à contrôler les lignes de livraison, elles synchronisent et standardisent le processus d'entrepôt. Elles constituent donc la base de toutes les transformations".