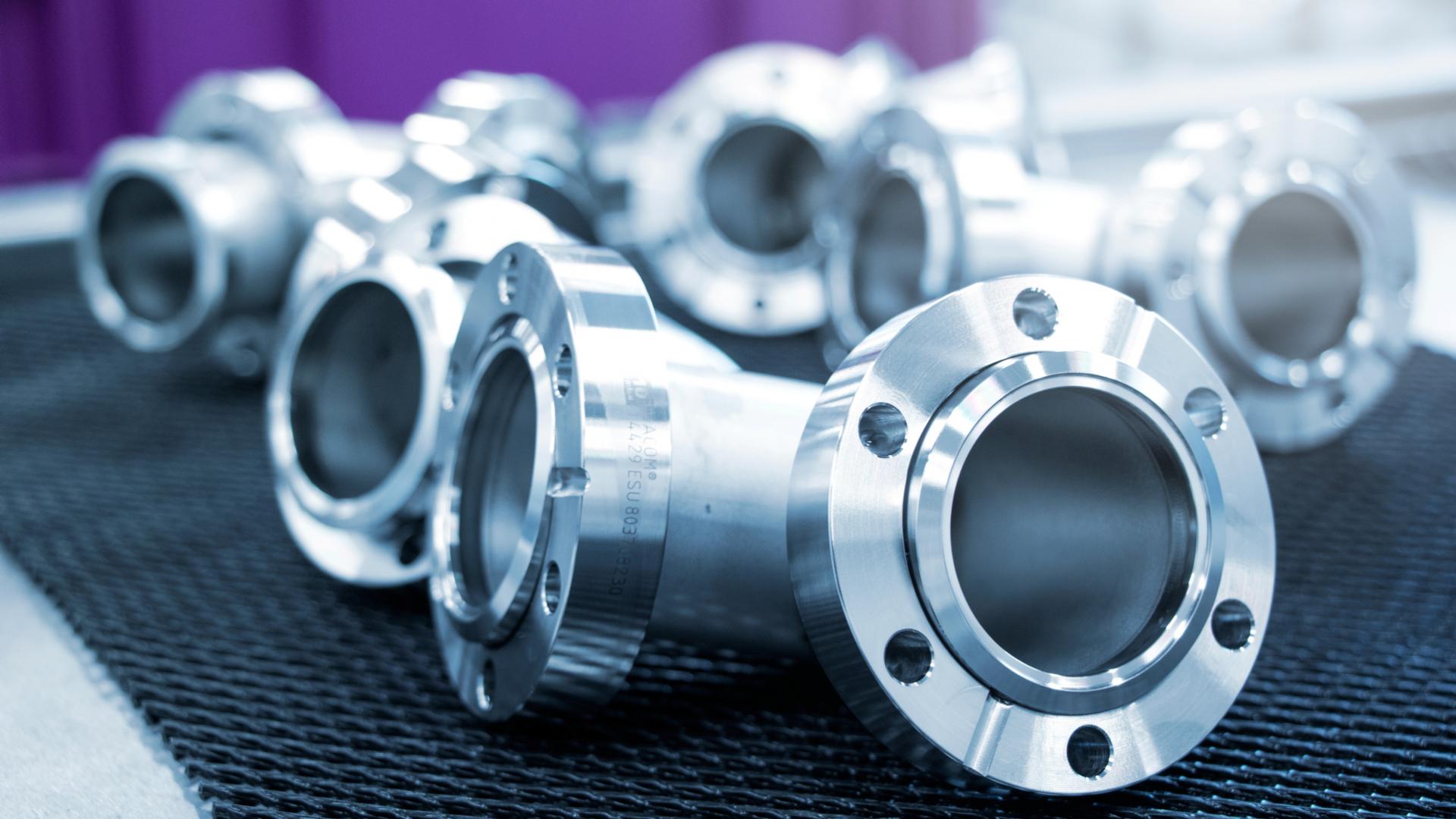
Logistika splývá s výrobou
„Čím víc součástí jsme vyráběli a čím byla výroba komplexnejší, tím víc se z ní stávala jakási černá díra“, vzpomíná Kevin Mahler, COO u společnosti VACOM GmbH. Podnik se sídlem v Jeně, založený v roce 1992, vyrábí komponenty pro aplikace ve vysokém až ultra vysokém vakuu. S úspěchem, neboť potřeba ultra čistých vakuových součástí vzniká ve stále více odvětvích – například ve výzkumu, při výrobě čipů nebo pro povlakování optiky a displejů. Jen v uplynulém roce a půl přibylo v podniku víc než 100 lidí. Dnes VACOM zaměstnává kolem 350 pracovníků, shání lidi na dalších 120 pozic a patří k vedoucím evropským dodavatelům vakuové techniky.
Vysoce komplexní výroba
Razantní růst staví před podnik nové výzvy: Efektivně zvládat procesy a současně si zachovat přehled, to vyžaduje velké úsilí. „Naše výrobky jsou nanejvýš složité – sestávají částečně z několika stovek součástek“, vysvětluje Mahler. Většinu těchto součástek, například příruby, vyrábí VACOM sama – ve výrobních sériích až po 1000 kusech. „Komplexní výrobky, jako naše kulové nebo válcové vakuové komory, zhotovujeme na míru podle požadavku zákazníka.“ Typická velikost série tu činí maximálně deset kusů – Kevin Mahler tomu říká „sériová výroba prototypů“. Napůl hotové díly se ve výrobním procesu opakovaně přesouvají mezi jednotlivými pracovními kroky a tvářecími stroji sem a tam. Klasická výrobní linka proto není možná. Ani klasické systémy řízení výroby, jako kanban, nelze u VACOM použít, protože na jedné stanici je zřídkakdy zapotřebí stejný díl. Proto museli
pracovníci VACOM na začátku zpracování zakázky kompletně přichystat potřebný materiál a následně jej rozdělit na různé stroje a pracoviště.
Vyhledávání materiálu zabírá příliš mnoho času
„Poslali jsme do výroby polotovary a suroviny a dostali koncový produkt“, popisuje Mahler. „Věděli jsme sice, co se ve výrobě děje, ale netušili jsme, kde přesně se v danou chvíli jednotlivé materiály nacházejí.“ VACOM proto mohla jen obtížně reagovat na změny. „Naši zaměstnanci trávili stále více času tím, že vyhledávali součásti a dopravovali je na potřebné pracoviště. To zašlo nakonec tak daleko, že jsme za směnu měli minimálně jednoho kolegu, který nedělal nic jiného, než hledal materiál“, shrnuje to Kevin Mahler. Při výrobním týmu, který tehdy tvořilo 50 lidí, to bylo jednoznačně příliš mnoho.
Na cestě ke Smart Factory
VACOM se proto rozhodla, že výrobu změní na „Smart Factory“. Za tím účelem vytvořil Mahler se svým týmem nejdřív průhlednou továrnu: Na digitálním vyobrazení definovali, jak mají jednotlivé komponenty procházet výrobou a jaké pracovní kroky je přitom třeba provádět. „Teprve pak bylo zřejmé, kde se co nachází, co se právě dělá a kdo pracuje u kterého stroje“, objasňuje Kevin Mahler. Tato data vytvořila základ pro druhý stupeň na cestě k inteligentní továrně – stvoření reakceschopné výroby. Za tím účelem se VACOM spoléhá jednak na Manufacturing Execution System (MES), výrobní informační systém HYDRA společnosti MPDV Mikrolab GmbH, a jednak na Warehouse Management System (WMS), systém řízení skladu viadat od viastore SOFTWARE, který již spravuje stávající automatický sklad. Společná správa dat prováděná WMS, MES a SAP ERP umožňuje rychle reagovat na změny ze strany zákazníka nebo nové potřeby.
V roce 2019 následoval další stupeň ke Smart Factory: závod se samočinnou regulací. Kevin Mahler nejdříve zamýšlel průběžnou automatizaci výrobní logistiky a následkem toho využívání přepravních robotů. Za tím účelem se obrátil na viastore: „Odborníci mi vysvětlili, že nasazení přepravních robotů je ve viadat standardem.“ Ovšem v tomto konkrétním případě šlo o logistické zásobování výroby. To znamenalo, že WMS musí po každém pracovním kroku obdržet příkaz od MES, aby mohl příslušně roboty řídit. Takové propojení MES a WMS zatím standardně neexistovalo. Ale aby viastore umožnila právě takovou integraci, uzavřela již nějakou dobu předtím strategické partnerství s MPDV – oním vývojovým střediskem software, od něhož pochází MES u VACOM.
Propojení WMS a MES
Systém viadat disponuje v aktuální verzi standardním rozhraním, které umožňuje výměnu dat s HYDROU. „Přes toto rozhraní se dají s viadat propojit i další běžná řešení MES“, vysvětluje Simon Kallinger, který pro viastore u VACOM projekt řídil. Za tím účelem si VACOM všechny zúčastněné pozval k jednomu stolu. Společně si definovali, jak je možné do detailu integrovat systémy a jaké klíčové kompetence mají být splněny. Výsledkem byla úzká integrace obou systémů, „přičemž WMS, MES a SAP jsou rovnocennými partnery a mají svá vlastní rozhodovací oprávnění“, zdůrazňuje Kevin Mahler. „To znamená, že MES a WMS samočinně předávají informace, aniž by potřebovaly procházet přes SAP.“ Automaticky regulují úkoly pro cca 45 pracovních stanic ve výrobě a šest přepravních robotů.
Dva systémy, které se regulují samy
SAP je v souhře systémů nakonec odpovědný již jen za generování zakázek a předává výrobní příkazy s kusovníkem HYDŘE. MES přebírá podrobné plánování – jaký stroj, jaký nástroj, jaký materiál a jací pracovníci – a předává následně kusovník včetně časového rozvrhu na viadat. Ten zase generuje zásobovací zakázky pro příslušné logistické potřeby na jeden pracovní postup, které jsou uloženy ve vyrovnávacím skladu výrobní haly. Tím se redukuje potřebné místo na meziuskladnění na jednotlivých pracovních stanicích. Teprve krátce před zpracováním udělí WMS přepravní příkaz a robot přiveze materiál na pracovní stanici. Zde je znovu uložen v malých regálech, než jde do konečného zpracování. Tak je možné optimálně využívat kapacity na obráběcích strojích. Pracovník podá hotovou zakázku do výstupního vyrovnávacího zásobníku a naskenuje ji. To zase vyvolá instrukci ve viadat, takže robot zboží následně přiveze do skladu supermarketu nebo přímo do další pracovní stanice. „Systém viadat se tedy zapojuje do akce mezi jednotlivými pracovními kroky, a MES a WMS spolu nepřetržitě komunikují“, vysvětluje Kevin Mahler. Simon Kallinger to doplňuje: „Realizovali jsme tak pravý koncept just in time. Systém viadat ví, jaké jsou kapacity na zásobních místech a může tak naplánovat, aby byla tato místa průběžně doplňována a materiál byl včas k dispozici před příštím pracovním postupem.“
Výhra pro zákazníky i pracovníky
Kevinu Mahlerovi je jasné, že to s sebou přinese výrazné zvýšení efektivity pro zaměstnance na pracovních stanicích. „Kolegové si nebudou muset hledat materiál, ani tahat bedny. Všechno, co potřebují pro výrobní krok, se jim přiveze přímo na pracoviště. Sami musí už jen připravit zařízení a obrábět.“ Tím jsou zbaveni namáhavých a neoblíbených činností a dělají výhradně to, k čemu byli vyškoleni a co je baví. To ale neplatí jen pro zaměstnance u strojů, nýbrž i pro další pracovníky, kteří se starají o organizaci a chod výroby. Díky transparentnosti, která vzniká v důsledku spojení WMS a MES, vždy vědí, kde se který materiál nachází, jak jsou stroje vytížené a jak daleko pokročilo zpracování výrobku. „Jejich pracovní zatížení se mnohokrát sníží“, prohlašuje s důvěrou Mahler. „Teprve ve chvíli, kdy systémy nebudou schopné vyřešit určité problémy – například když bude nějaký díl ve skladu chybět, – bude zavolán na pomoc člověk. Zaměstnanci už také nebudou využíváni jako tahači beden, nýbrž se stanou řešiteli problémů.“
Celková výkonnost výrazně stoupla
Z chytré výroby mají prospěch i zákazníci VACOM, jak vysvětluje Kevin Mahler: „Je optimalizovaná evidence zásob a masivně se snižují prostoje a ztrátový čas. Naše kapacita stoupá a průběžné doby pracovního cyklu klesají. Kromě toho můžeme rychleji zásobovat naše zákazníky.“ Už jen díky závodu s automatickou regulací stoupla OEE, Overall Equipment Effectiveness, celková efektivita zařízení, ve výrobě VACOM o pět až deset procent. Kevin Mahler vychází z dalších pěti až deseti procent, až bude současná optimalizace ukončena, a je si jistý: „Jen ten, kdo dokáže rychle a pružně reagovat na přání zákazníků, aniž by vznikl chaos, zůstane dlouhodobě úspěšný na trhu. Dívat se na výrobu a logistiku jako na dva rozdílné páry bot, to už v budoucnu nebude fungovat.“