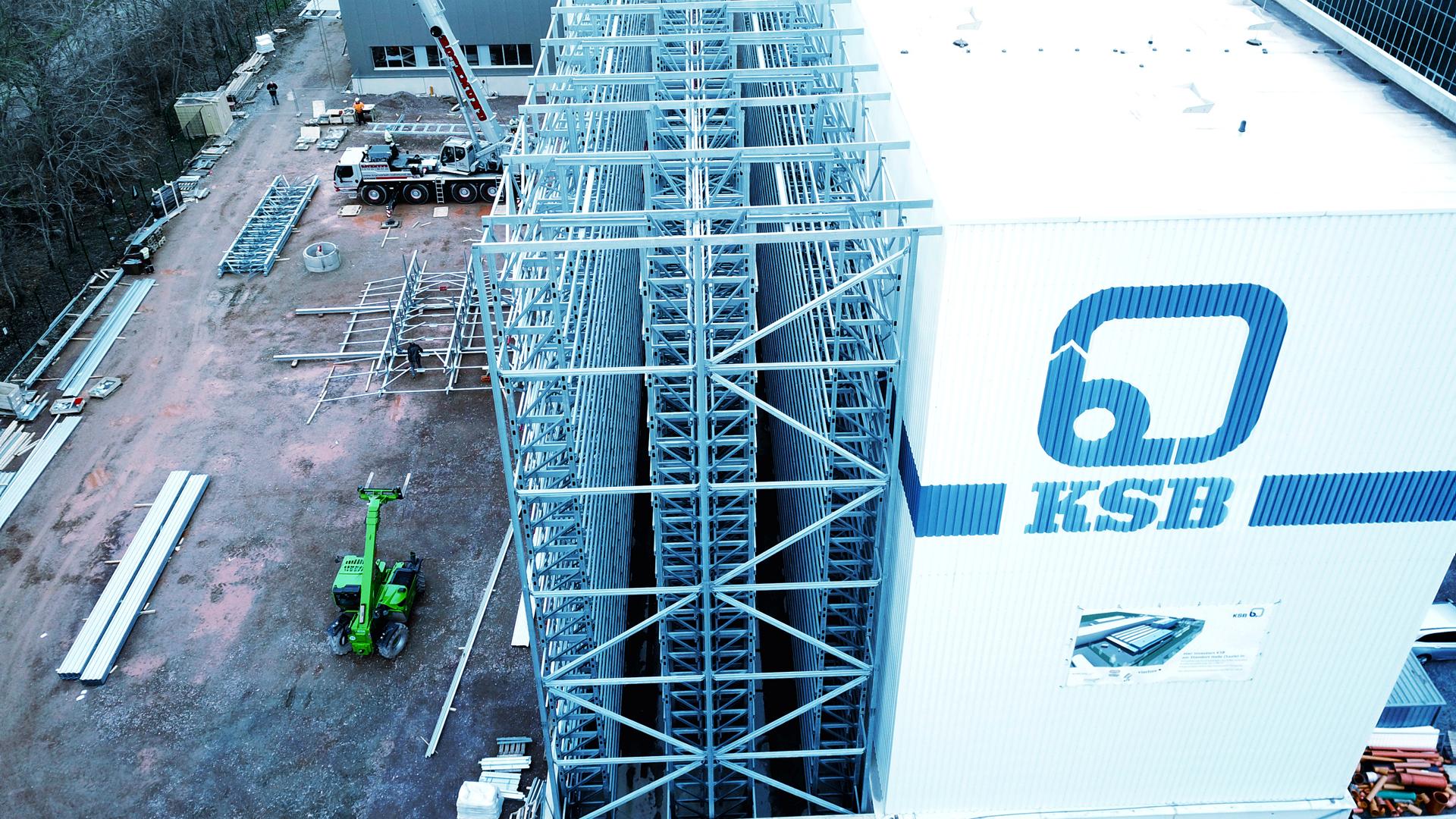
25 percent performance increase achieved with great steps
A fill rate of over 97 percent, little space for material buffers in production, and exacting customer expectations – KSB’s manufacturing warehouse in Halle (Saale), which went into operation in 1995, had reached its limits. “The Halle location is KSB’s competence center for pumps and submersible motors for our water and wastewater technology division,” explains Plant Manager Frank Aschenbach. Driven by the growing world population, urbanization and increasing environmental awareness, this is a real growth market. “We produce around 12,000 pumps and 16,000 submersible motors annually – with a high level of vertical integration and in an extremely wide range of variants. However, with this number of units we are now approaching the limits of our capacity.” KSB is therefore investing around ten million euros in warehouse logistics and mechanical production in Halle by 2022.
“In order to be able to embrace this growth and meet the increasing demands of our customers for short delivery times, we are making structural improvements at this location,” adds Marcel Schwarze, KSB Project Manager for the plant expansion called “Halle 2020”. In addition to expanding the 24,000 square meter production area, procuring larger production machines and optimizing work processes, the modernization and expansion of the automated unit-load system is a key measure in achieving this goal. Supplying the machines and production lines with raw materials and semi-finished parts, it is the heart of production.
Growth pushes logistics to its limits
Smoothly functioning and efficient warehouse and material flow processes are essential for the company. After all, hardly any of the pumps manufactured are alike – which is why KSB does not produce them for stock, but rather on an order only basis before shipping them to customers immediately upon completion. Raw materials and semi-finished goods are stored in pallet boxes. “At peak times, only very few of our more than 5,900 pallet storage locations were available,” says Oliver Fuchs, Warehouse Manager at the Halle site, describing the situation with regard to the automated unit-load system. “To create space, we regularly had to repack and consolidate the goods. It got to the point that during the late shift two employees were busy doing this for several hours to ensure there would be some space available the next morning.” This was the case even despite the fact that the company had already rented external storage capacity in the neighborhood.
An additional factor was the streamlining of the production, as Fuchs explains: “In the past, we used to store material for two days at buffer locations in production.” But as orders increased, this space was needed for manufacturing operations. Today, Oliver Fuchs’ team must provide the material to production within just four hours or even less time. “Due to the massive capacity utilization of the warehouse, work in logistics has increased by 30 to 40 percent,” says Norbert Fisch, KSB’s Process Optimizer who ensures on-time delivery at the Halle location. “We want to and must continue to grow in the future,” says Fisch. “Therefore, the question was how we could improve things as quickly as possible.”
Decision to expand and modernize the system
The first idea was to upgrade the warehouse management system. To date, the more than 20-year-old viadat 5.4 Warehouse Management System (WMS) has been used to manage the warehouse and material flow – software developed by Stuttgart, Germany based intralogistics specialist viastore, who had also built the automated unit-load system. This WMS version does not include many of the functions that are standard in the current generation 9.1. “With the upgrade, we could have made better use of the available space,” explains Fisch. But it soon became clear that a new WMS alone would not be sufficient because the processes in the conveyor system transporting the material from the automated unit-load system to the picking stations also proved to be a bottleneck with regard to the growing order situation.
KSB therefore decided to expand the triple-aisle automated unit-load system by adding two more aisles comprising a total of 4,600 storage locations as part of the plant restructuring, as well as to optimize the conveyor system, replace the controllers and convert to the Profinet bus system. “It was important to us that we implemented the entire reconstruction without interfering with production,” emphasizes Fisch. The order was assigned to viastore – not just because the company had already built and regularly modernized the original system, as Norbert Fisch explains: “We chose viastore because the company not only has the necessary system expertise but can also provide the control system and the most modern software for warehouse and material flow. In addition, viastore accompanied us all the way from the planning stage through simulation and process optimization to the implementation stage and assigned an experienced project manager to us who gave us a feeling of security at all times. This allowed us to concentrate on our core tasks.”
The goal: 25 percent increase in performance
KSB defined the goal of the expansion and modernization as a 25 percent increase in performance. In collaboration with the KSB team, viastore developed various scenarios and checked them for practicality and profitability with the help of extensive simulations. “In the end, we decided on the concept that delivered the best results,” explains Norbert Fisch.
Thereupon Martin Ziemann, Project Manager at viastore SYSTEMS, set about the detailed planning – always bearing in mind that on-going production should not be interrupted. “The first thing he did was draw up a detailed schedule with all the necessary work steps. All tasks, including fire protection and facade construction, were to some extent scheduled to the minute,” remembers Norbert Fisch – and he is still amazed: “This schedule with a total of 189 process steps had to be adjusted only once during the whole course of the project – and that was solely because of problems with the construction terrain.” Marcel Schwarze adds: “Each individual reconstruction step was thus determined in advance, and everyone involved knew exactly which step had to be implemented and when.”
Completing the retrofit step by step
“Only with this kind of approach is it possible to avoid production downtimes,” explains Swen Mantel, who is responsible for viastore’s retrofit business. “With such measures, you have to plan step by step – especially in order to minimize the risk of interrupting on-going operations.” To keep all processes running, viastore repeatedly implemented temporary interim solutions. “We modernized the three picking stations one after the other. First the conveyor system was rebuilt, then the new drives were installed, followed by the wiring. In the meantime, we converted the third picking station into a goods receiving station,” Norbert Fisch explains.
Thanks to new branch lines, the picking points can now be supplied with material independently of each other. In addition, each station has adequate buffers. “Our aim was to ensure that the employees always have sufficient material available instead of having to wait for it, as was the case until recently. This is the only way to achieve a high picking rate,” explains Marcel Schwarze. “The renewal of the conveyor system and the restructuring of the tracks has already led to a significant increase in system performance,” states Norbert Fisch. “Thanks to these measures, we would be able to increase the performance of the warehouse by another 40 percent before reaching the mechanical capacity limits.”
New viadat results in additional efficiency increase
The final step of the expansion was the upgrade of the warehouse management system to the new viadat 9 version. “To be able to make optimal use of the software, we first of all had to revise all processes,” sums up Christian Fehlau, Sales Manager at viastore and head of the project. viadat can be operated intuitively and offers more than 2,500 functions even in its standard version.
“The ABC categorization of the warehouse items was particularly important to us in order to optimize the travel paths of the automated storage and retrieval systems,” emphasizes Warehouse Manager Oliver Fuchs. “This enables faster access, increases the number of picks and thus generates a higher picking performance.” In addition, the current version of the warehouse management system offers much better evaluation options. “With the previous, more than 20-year-old version, we had to create our evaluations in Excel, which was very time consuming. With viadat 9, we get the desired figures on an individual dashboard with just one click,” Fuchs explains. “This way, we have all developments in view and can actively influence them in a forward-looking manner. This not only saves time, but the system is also optimally utilized and production can be more easily linked to logistics,” points out Norbert Fisch.
Completion ahead of schedule
The new warehouse was commissioned one week ahead of the actual deadline. Norbert Fisch is still impressed: “The fact that the coordination worked so well despite the many people involved in the project is simply remarkable and illustrates why viastore is one of the leading companies in the industry.” However, viastore not only completed the project ahead of schedule, the company also successfully implemented the targeted 25 percent performance increase. Plant Manager Frank Aschenbach draws a positive conclusion here as well: “Although we operated our plant at peak capacity during the modernization and conversion phase, the project was completed without any loss of production. That is a truly outstanding achievement.”