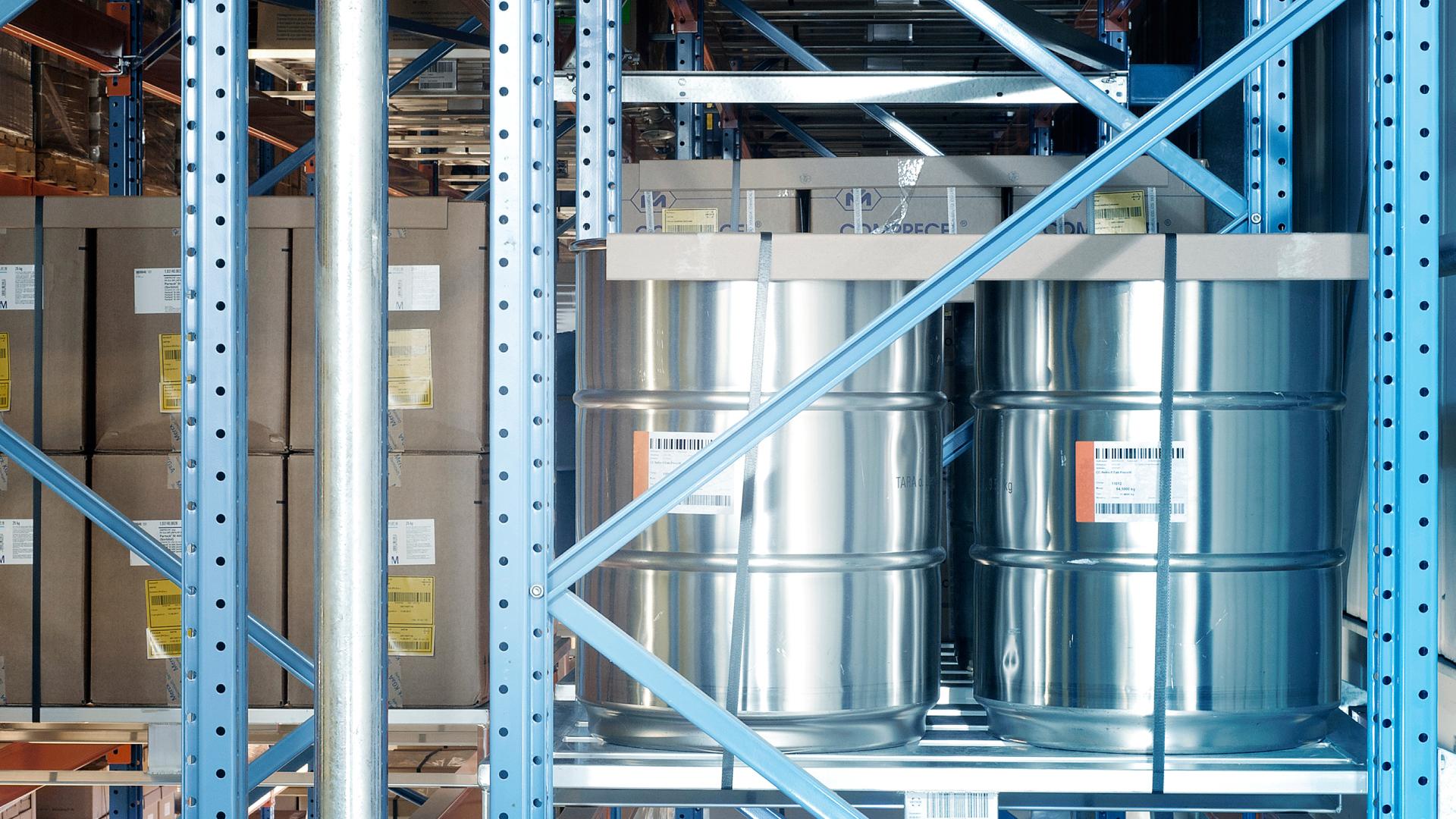
Automated warehouse enables pharmaceutical manufacturer Medice to use energy-efficient intralogistics
Benefits
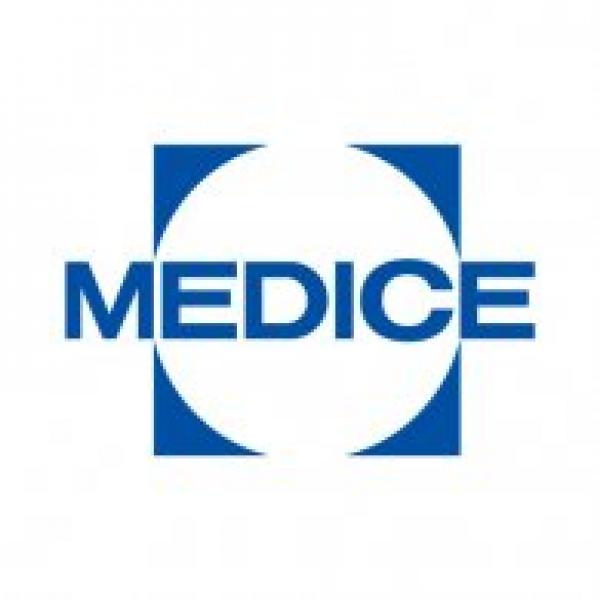
- High flexibility and speed
- Secure processes created
- Energy-efficient intralogistics achieved
- Free space created through reduced inventory
Why did Medice decide on an automatic warehouse?
The demands of the pharmaceutical industry on intralogistics are particularly high: all products and processes must be documented and the availability of goods should be 100%.
Within five years, Medice has more than doubled its turnover - but the warehouse has reached its capacity limits. The storage and retrieval processes were too slow; production often had to wait several hours for raw materials to be delivered from the warehouse. The employees managed creating reserves and hoarding goods in production or shipping - an inefficient process that also took up a lot of space.
In order to resolve the warehouse bottleneck and efficiently implement its international growth strategy, Medice decided to work with viastore to build a modern, fully automated high-bay warehouse and implement the viadat Warehouse Management System (WMS).
What does the automated warehouse contain?
A three-aisle, double-deep and fully automated pallet high-bay warehouse (HBW) with 4,272 storage locations was built. It offers sufficient space for all finished products and has a racking row in which the raw materials and primary packaging materials are stored on aluminium pallets that meet the high hygiene requirements of pharmaceutical production.
The new warehouse is built directly adjacent to the existing high-bay warehouse and therefore had to be integrated into the existing plant structure. The connection of the existing warehouse and the new automated warehouse to the production and the also newly built dispatch center was planned on different levels: A cross-traversing carriage on the upper floor serves as a central connecting element between goods receipt, storage and production. The connection to the dispatch building is made underground via a 120-meter-long tunnel, also with a cross-traversing carriage.
The internal warehouse and material flow processes are administered and managed by the viadat Warehouse Management System which is also connected to the company's ERP system. viadat monitors best-before dates, stores and retrieves material in and out of the warehouse with batch accuracy, manages goods receipts and warehouse movements and documents every movement or change in detail. The WMS thus ensures seamless inventory management for the company. In addition, various access authorizations can be assigned within the system.
- Three-aisle fully automatic pallet high-bay warehouse
- Double-deep storage with 4,772 storage locations
- Three viapal stacker cranes with telescopic fork
- Own rack lines with aluminium pallets for products with the highest hygiene requirements
- Direct connection to the existing warehouse and dispatch center
- Two transverse transfer cars and four vertical conveyors
- Twelve high-speed and three fire protection doors
- Warehouse management with WMS viadat
What is the benefit of the automatic warehouse?
With the fully automated warehouse, Medice benefits from high flexibility, speed and greatly increased process reliability. Inventories in the production areas have fallen significantly which has freed up space that can be used productively again. Thanks to the faster and optimized workflows, the goods requested internally are on site within a few minutes.
With the automated warehouse, the company benefits from energy-efficient intralogistics: the climate required for the storage of pharmaceutical production is achieved by underfloor heating and natural ventilation - and not by installing an energy-intensive air-conditioning system. In addition, various measures such as energy recovery, optimized travel paths of the stacker cranes or energy-efficient drives can save more than 30 percent energy in the warehouse.